What would be the environmental impact of my DIY project? This is what Imme Groet, Senior Expert Sustainability and Sustainable Construction, wondered. Imme re-upholstered the cushions of her sofa herself. Read how she tackled this project and the impact calculation she made. Spoiler: making it yourself has a much lower environmental impact than buying new.
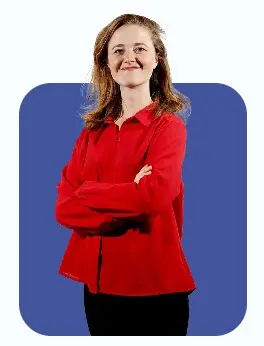
The perfect winter project: making new cushions for my sofa
When I moved house a while ago, my grandparents gave me a sofa they no longer needed. It’s a lovely little couch, just long enough for someone my size to stretch out on. It was a full designer sofa with leather cushions.
But after 50 years, heavy use, and several moves, the cushions were completely worn out, with large holes in the leather. This was the perfect winter project: while it was cold and dark outside, I decided to make new cushions for the sofa.
While working on the cushions, I started wondering about the environmental impact of replacing the covers versus buying a new sofa. How much material does this save? As a hobbyist, I calculated the CO₂ emissions from my DIY project. I was also curious to compare this environmental impact to that of purchasing a new sofa.
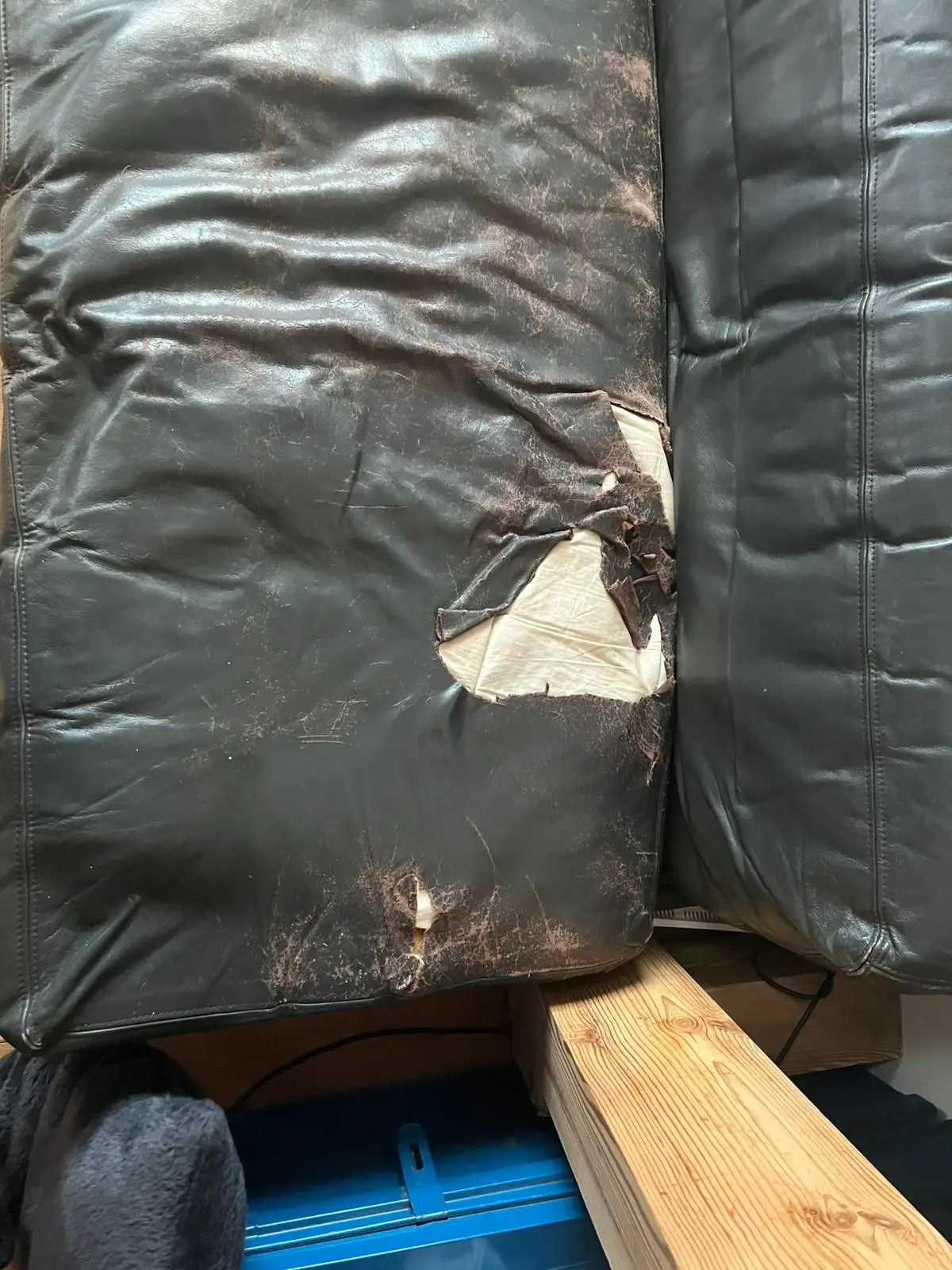
What is the environmental impact of my DIY project?
To answer this question, I calculated the CO₂ impact resulting from repairing the cushion covers. I only replaced the cushion covers; the foam and zippers were not replaced and will be reused.
The materials used to replace the cushion covers are as follows:
- 2.60 meters by 1.50 meters of linen fabric
Upholstery linen, 500 g/m²
For this sofa, 2 kg of linen was needed
- 120 meters of polyester thread
50 meters = 1 gram, so 120 meters of polyester thread is 2.2 grams
- 12 sheets of A3 paper
A3 = 420 x 297 mm
80 grams per m²
1.5 m² of A3 paper = 120 grams = 0.12 kg of paper
Next, I calculated the energy consumption, considering the following:
- A few hours of sewing machine use
- Half an hour of ironing
With these inputs, I arrived at the following environmental impact:
- Environmental impact of the linen: 24 kg CO₂-eq
- Environmental impact of the thread: 0.026 kg CO₂-eq
- Environmental impact of 0.12 kg of paper: 0.122 kg CO₂-eq
This results in a total material-related environmental impact of 24 + 0.026 + 0.122 = 24.148 kg CO₂-eq.
Then, I calculated the environmental impact of the consumed energy:
- Iron: 750-1100 watts -> 30 minutes, equals 0.5 kWh
- Sewing machine: 100 watts -> 5 hours, equals 0.5 kWh
- I know that 1 kWh corresponds to an environmental impact of 0.649 kg CO₂-eq.
Adding up both categories of environmental impact, we get 24.148 + 0.649 = 24.8 kg CO₂-eq, with the vast majority of the impact coming from the linen.
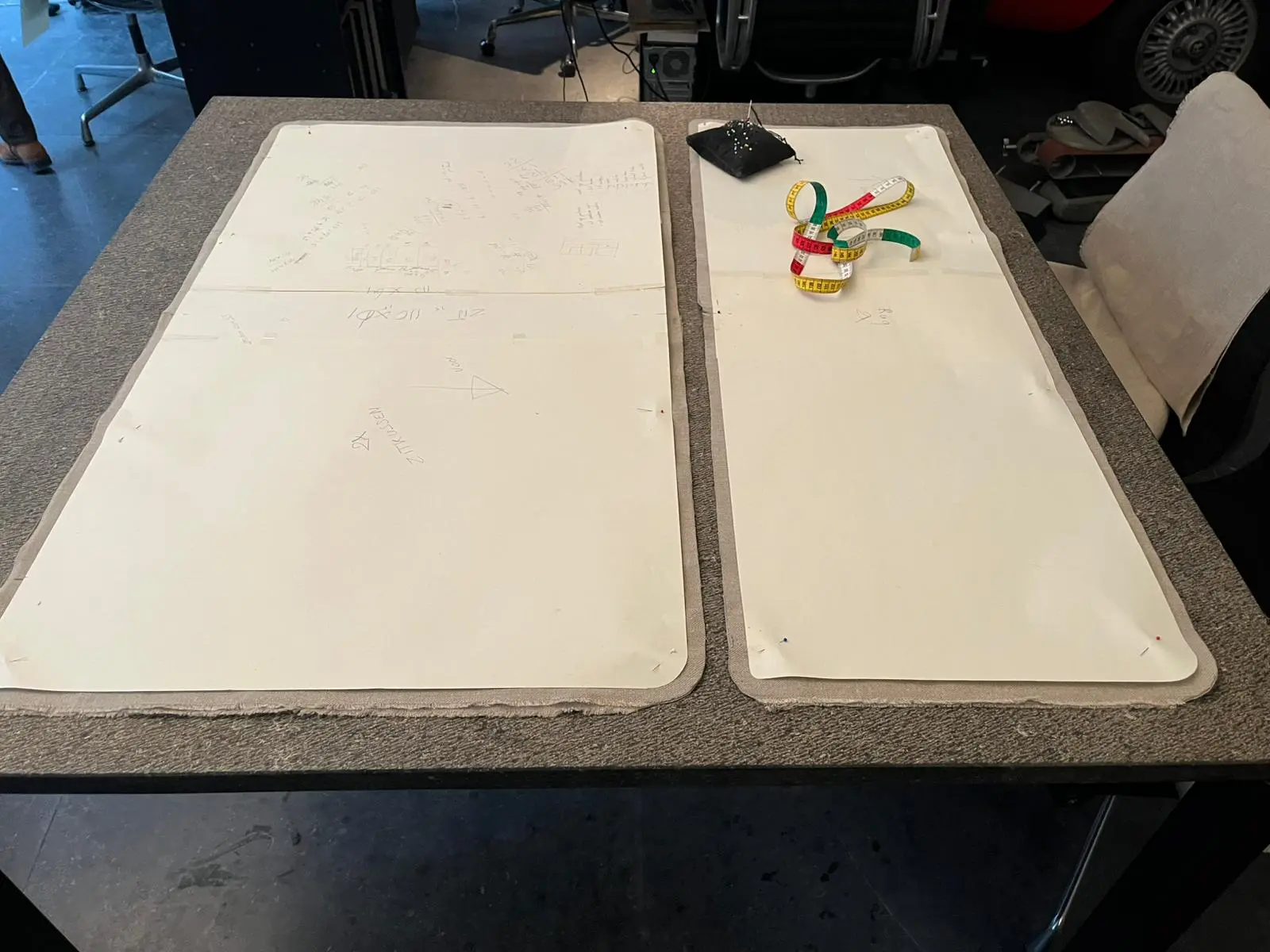
And how does the environmental impact of my DIY project compare to buying a new sofa?
A new sofa has an environmental impact of approximately 210 kg CO₂-eq (for an average-sized two-seater sofa). I determined this impact by combining various LCA studies on furniture.
This means that the environmental impact of purchasing a new sofa is nearly ten times higher than making new covers for my sofa cushions myself.
How did I carry out this DIY project?
For those interested in how I replaced the cushions, I will outline the process and materials used below.
1. Determining the dimensions
I replaced the cushions together with my mother, and I realise how lucky I am to have a mother who studied fashion at art school. We started by measuring the cushions precisely—we needed fabric for the backrest cushions and the seat cushion.
Some parts could be reused, such as the zippers from the old cushions and the foam filling inside the cushion covers. These components were still in excellent condition. Additionally, the sofa is so comfortable that I absolutely wanted to keep the cushions.
2. Choosing the fabric
Next, we went to the Boerenbonthal in Weesp (which, in my opinion, is like a candy store). There, fabrics are stacked up to the ceiling. After some searching, we found a beautiful, thick linen fabric.
Together with the staff, we calculated the exact amount of fabric needed and determined how to cut each piece efficiently.
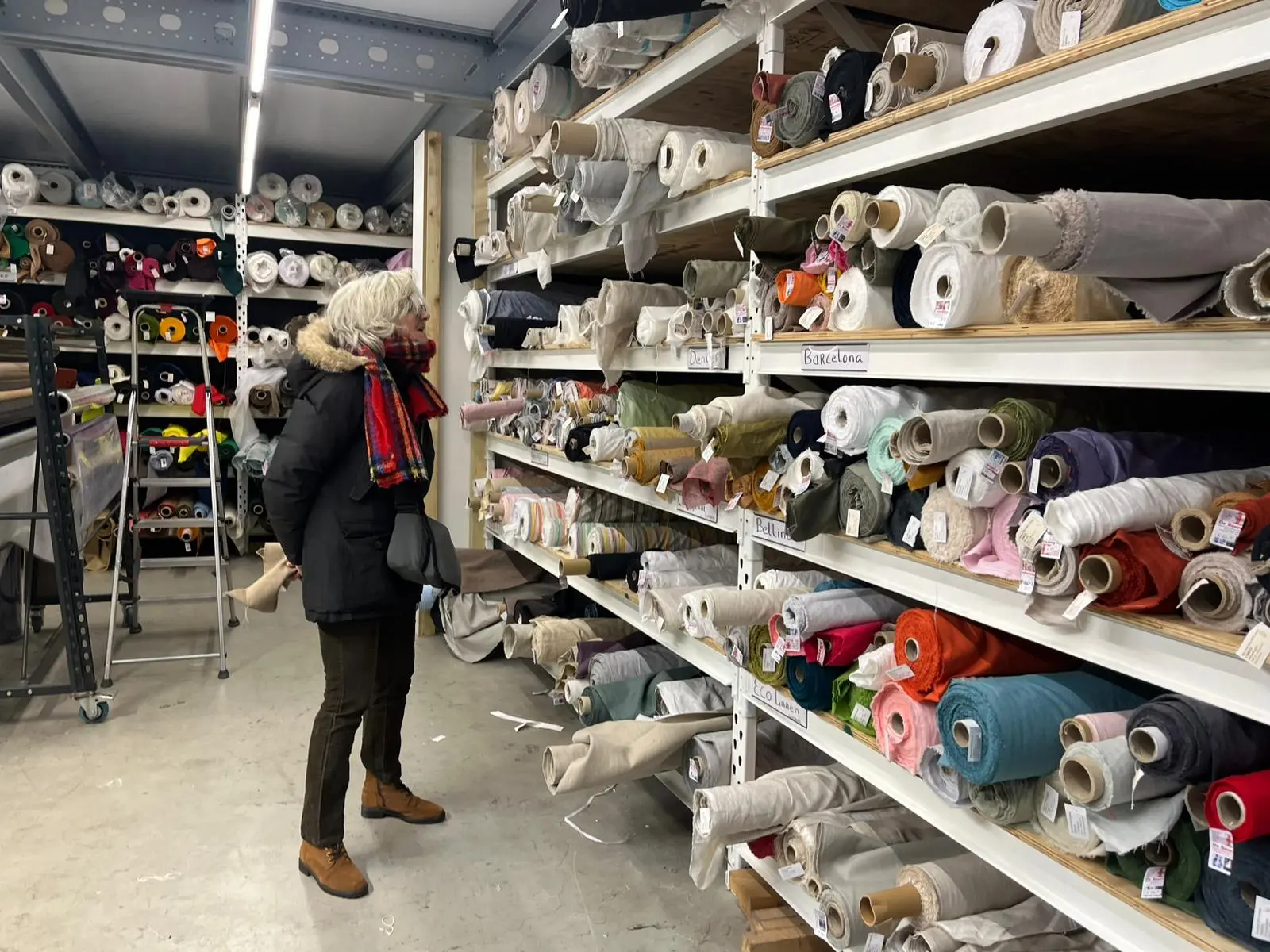
3. Making patterns and cutting the fabric
Then, we worked in our workshop to make the cushion covers. We started by creating the patterns. A cushion consists of multiple parts: the top, bottom, and sides. These patterns are made from paper, and each pattern piece matches the exact size of the fabric piece that will be cut later.
Next, we pinned these patterns onto the fabric and cut out the pieces. We cut an extra 1.5 cm around each edge—this extra fabric forms the seams where the cushions are stitched together.
4. Finishing the fabric edges and ironing
Next, we overlocked the fabric edges or used a zigzag stitch. This prevents the fabric from fraying. We did this along every edge, all the way around. Then, we ironed each piece to ensure the fabric was completely straight.
5. Pinning and stitching the fabric together
We then pinned the covers together and inserted the zipper. Once everything was in place, it was time to run the pieces through the sewing machine and stitch everything together.
We used a double stitch for extra durability. As a final finishing touch, we trimmed all the loose threads and tested the fit of the cushions.
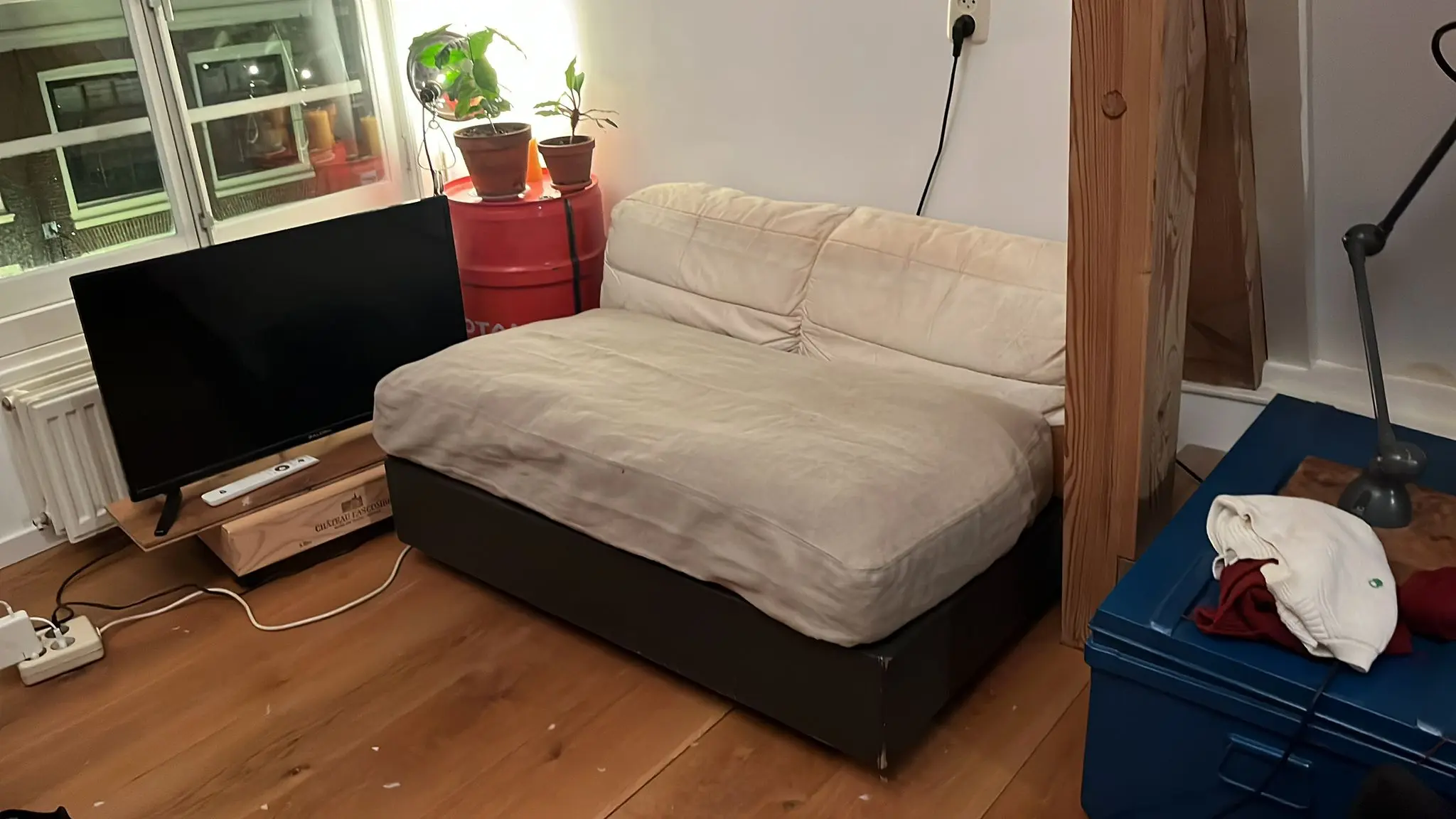
Balancing emotional value vs. economic feasibility
I am fully aware that this environmental impact calculation is not directly applicable to the economic reality of the interior design sector.
For me, this sofa has significant emotional value—it was a piece my grandparents loved and used for many years. I enjoy it every day and wanted to preserve it in my home.
That’s why I chose to repair the cushions instead of buying a new sofa (technically, this sofa has already exceeded its ‘economic lifespan’ three times, as the average lifespan of a sofa is 10–15 years).
We also invested nearly a full workweek in labor hours, which would be considered ‘unaffordable’ for such an old sofa in a commercial setting.
Moreover, I realise that not many people would find a DIY project like this enjoyable. Even for my mother and me, the process wasn’t without its fair share of frustration. But I truly enjoyed working together, making calculations, and ensuring the fabric was cut correctly.
Additionally, my mother already had essential tools such as a quality fabric scissors, a sewing machine, and a good iron—things that are not readily available in every household.
What this project taught me
One key takeaway from this project, which I will carry into my professional life, is that I want to place greater value on existing materials. It is frustrating that my emotional connection to my grandfather’s sofa feels so disconnected from the economic realities of the construction sector.
The built environment holds far more value than just its financial worth. Yet (and this is stating the obvious), our current economic models do not reflect this, and we seem to be moving even further away from recognising the value of existing materials.
Many business cases involving material reuse are nearly impossible to make financially viable. As a result, they often rely on idealistic motives from clients or contractors. Proposals have been made, including by Copper8, on how fiscal incentives for greener choices could work. However, there is still a long way to go before real action is taken.
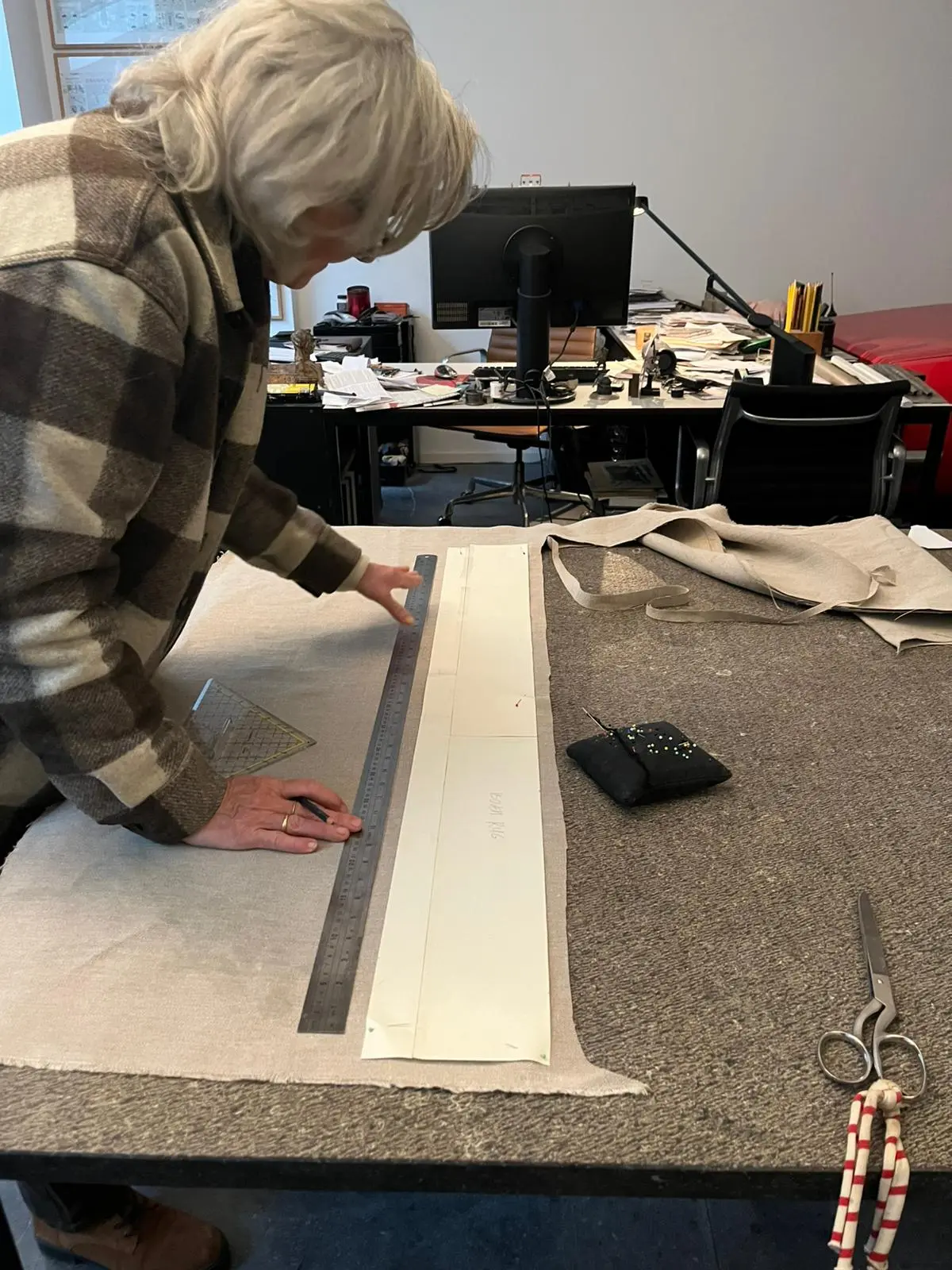
Tips for your own DIY project
Inspired to start your own fabric project after reading this article? There are plenty of places where you can find fabrics. We personally visited this shop: Boerenbonthal (in Weesp), where we also found threads and other sewing supplies.
Which fabric should you choose? If you want to consider environmental impact in your fabric choice, you can check the report I used for my decision: CE Delft’s report on the climate impact of one kilogram of dyed fabric.
I found it particularly striking that nylon has such a high environmental impact. The same applies to wool, but its impact calculation assumes sheep are kept purely for wool production rather than for meat consumption (unlike how leather’s environmental footprint is calculated).
Additionally, all natural textiles are renewable, making them a better choice than synthetic textiles.