HAHN Group is internationally leading in the production of recycled finished parts made from post-consumer plastics. Their product, Hanit® 100% recycled plastic, is a sustainable, robust, weatherproof, and maintenance-free solution. HAHN Group asked Hedgehog to perform a life cycle assessment (LCA) and following environmental product declaration (EPD) on their product, which insights will enable HAHN to quantify the environmental benefits. Noel Marques-Neves, Head of Operations, shares how he experienced our collaboration and what insights HAHN retrieved.
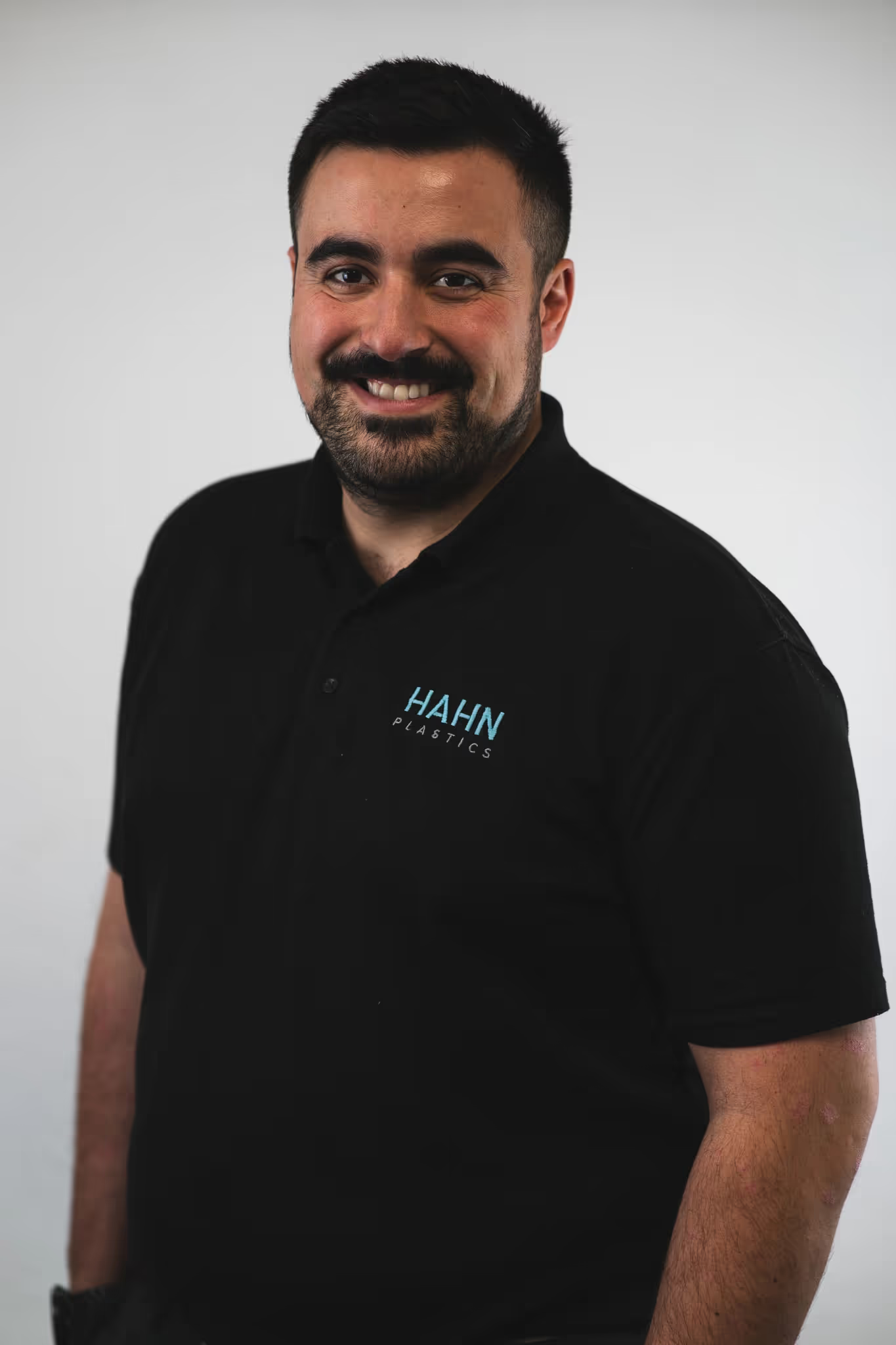
What made HAHN Plastics decide to start an LCA study?
As a company, we have the mission to preserve natural resources. We were looking for a way to get insight into how we are doing so. Both through the actual material that we use, and through the carbon footprint of our business.
As a manufacturer using recycled materials, sustainability is at the heart of our business. We were looking for a partner that could work with us and would help us understand how our products affect the environment in terms of its carbon footprint, through its whole life.
We operate in many sectors (construction, transport, equestrian, landscaping e.g.), having various clients. Overall, we noticed that clients are becoming more environmentally and sustainability-focused. They want to incorporate sustainability into their business, and are looking for clarification on the carbon footprints of their stakeholders. HAHN Plastics wanted to support its clients, enabling them to distinguish themselves as being sustainability-focused.
So the question came both from us intrinsically, as a company, and it was also driven by the trend we see with our customers.
Did you have any expectations upfront?
I didn't have much in-depth understanding of LCA’s before we started, and I was surprised how much information was needed to do the study. I felt like the guys at Hedgehog helped me understand why they needed certain data and the details to go into it.
During the process, I wasn’t overwhelmed since I was half expecting these amounts to ensure accuracy. And that was our main wish; to make it as accurate as possible. We didn't want to make any mistakes on that.
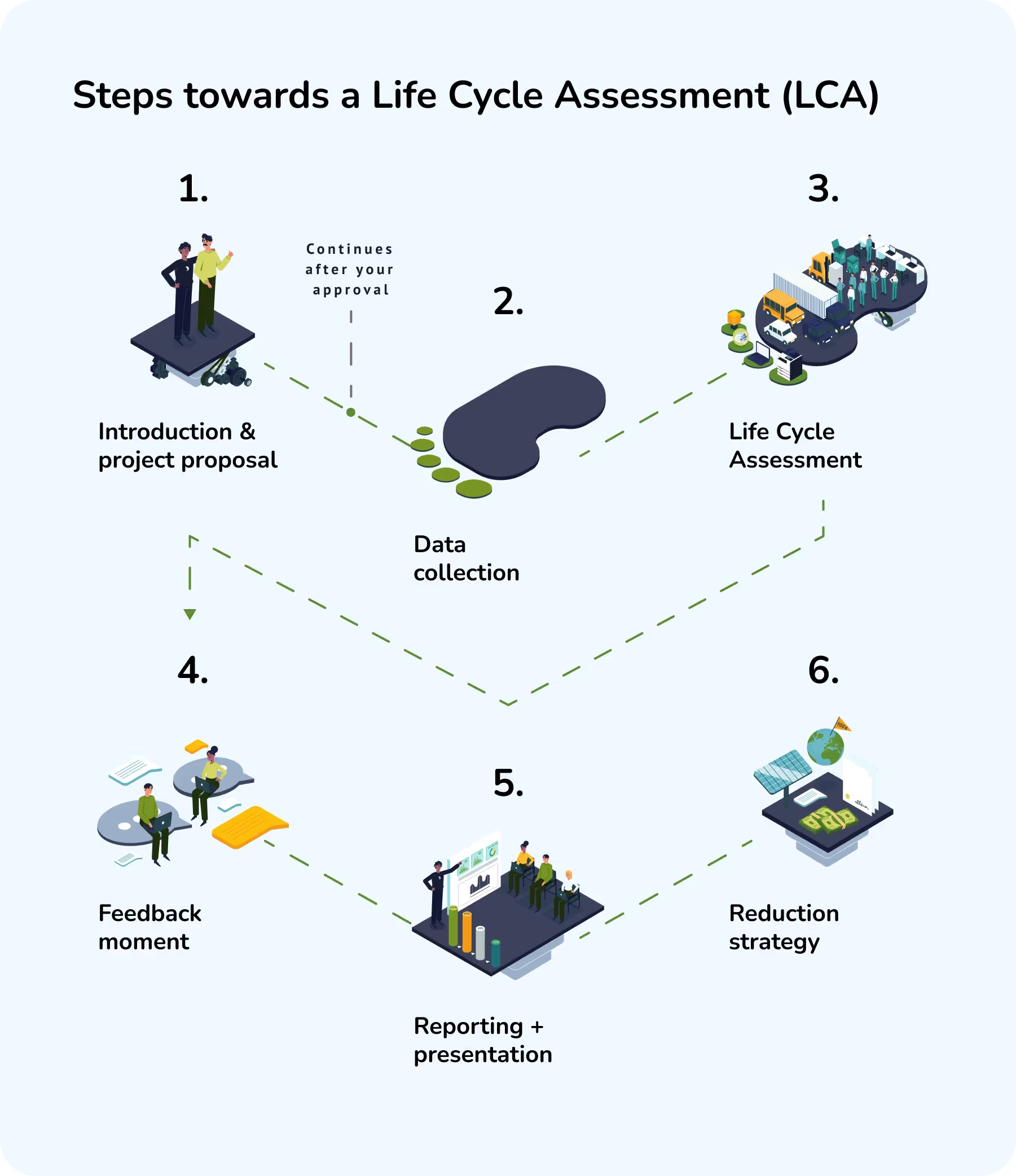
How was your experience of the process with us?
I feel that the process was made extremely simple, for what can be a very complex question. The team at Hedgehog put in place some really good tools to achieve that. Especially in helping us to collect the data in a structured way, and afterward in helping us to understand this data and the final LCA report.
We had a lot of contact; in the beginning, to set out the process that allowed us to then continue with the data collection on our own. We did some feedback calls back and forth, about things to improve and certain data that needed some clarification. The communication was excellent throughout the whole process, which helped it run very smoothly.
I was extremely surprised at how quickly the process happened and also how smoothly it went; it was clear to us how we could do things, and there weren’t many adjustments needed later on.
Noel Marques-Neves: “The collaboration with Rik and Saro was really good. They were very good at helping me understand the process, and more than happy to help us with any questions. Feedback was quick and calls were set up very easily to talk for 15-20 minutes, so we could carry on. Overall, Hedgehog was very supportive throughout the process.”
Who worked on the LCA internally?
Since we needed to collect data over the whole organisation, different teams worked on this in collaboration. We had our supply chain team do all the data analysis for transportation and materials. Then we had myself and a few of my operations team members working on the energy usage in manufacturing and the processing. In total, we worked with a team of around ten people contributing to collecting and validating the data.
And what was challenging along the way?
A challenging thing was understanding the allocation of energy to different processes. Because we didn't have energy monitoring at different levels, we just knew the total amount of energy used and the impact of the whole product made.
So we had to make some calculations; on which equipment used what amounts of energy, and whether certain pieces of equipment were more efficient than others. That was quite interesting to do and provided us with exactly the energy consumption across all production equipment, which was extremely useful information that was gained from this process.
I think the other challenge was just making sure that we were as accurate as possible, and we included everything that we could think of. That could be quite a complex question. For our freight data, for example, we had to trace where the materials were purchased from, how far they had traveled, how they traveled, and how this impacted our carbon footprint.
That was a lot of detail to go through, but helped us understand how our product impact is formed as a whole.
What insights did you get from the report?
The biggest insight was in the impact of our energy consumption: we have a very energy intensive process. So the LCA study really highlighted this impact, caused by our energy usage.
We asked Hedgehog for recommendations on how we could improve this aspect by moving to renewable energy because previously we had a mixed energy supply including high carbon sources. Following the recommendation from Hedgehog we have moved as a company to 100% renewable energy, which has made a 75% reduction in our product's impact on climate change.
Hedgehog made different simulations for us, to facilitate us in changing to green energy. They simulated the estimated effect of this change, and we decided that it was the right thing to do as a business. Within some weeks we had all the insights, and this for me shows a quick and easy improvement that can be made to become more sustainable as a company.
Besides changing to green energy, our target is to reduce our overall energy usage by 10% in 2024 by engaging our team in energy saving projects across the business. Understanding the environmental impact of manufacturing our product has given us the drive to continue to reduce this further.
The LCA also showed us the impact of transportation, which made us look at trying to source materials locally and closer to our factory.
Rik Wessels, Senior LCA expert: "It was very pleasant to collaborate with HAHN; we truly felt their drive to become more sustainable. When the LCA study revealed that electricity had the greatest impact, HAHN immediately asked us for a solution. We calculated the energy mix from various green energy providers, and with that, HAHN made the switch and drastically reduced their impact. This is a great example of what an LCA yields: concrete and effective steps towards sustainability."